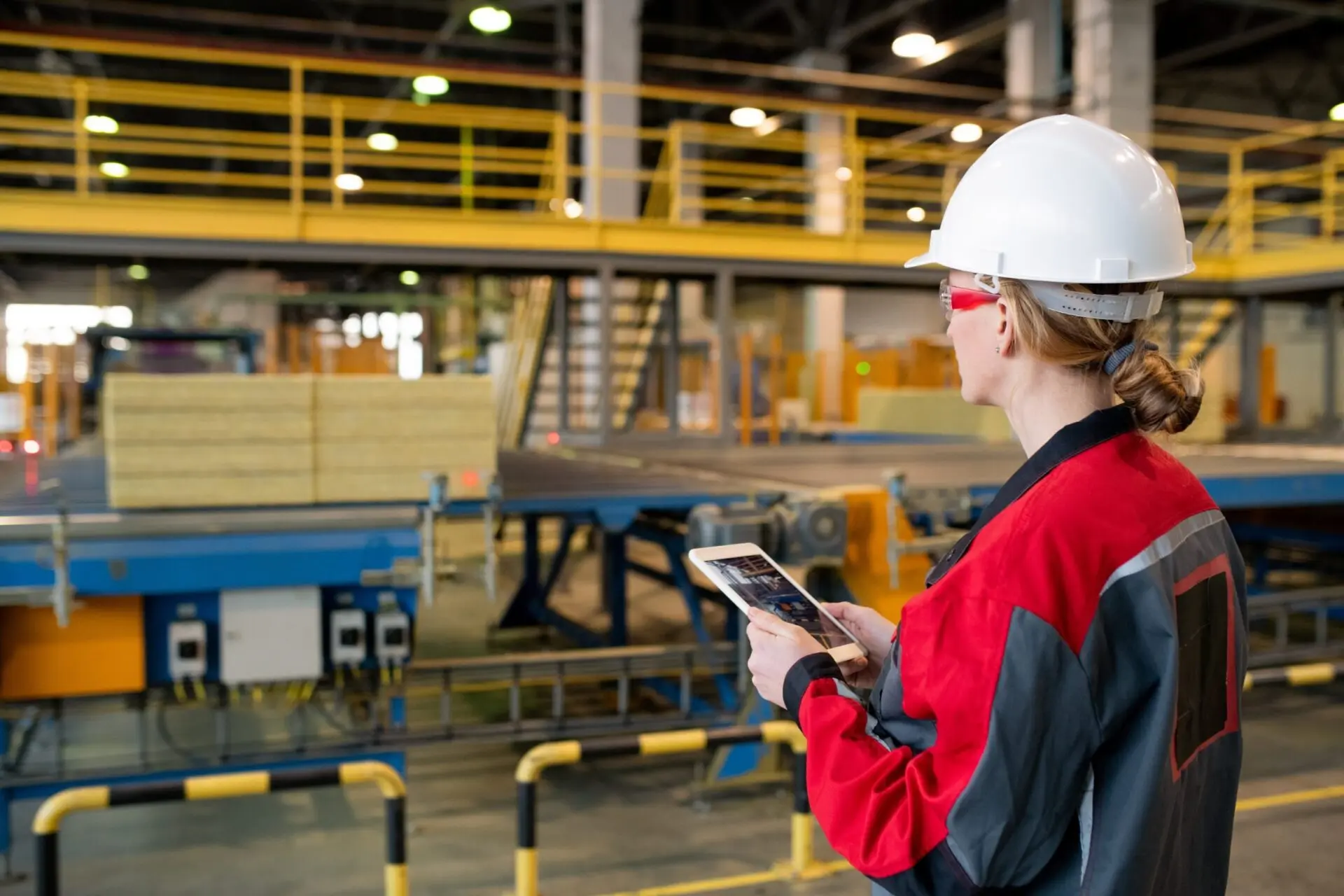
How much safer is the workplace today compared to a decade ago? According to the International Labour Organization, over 2.3 million workplace deaths occur annually worldwide, with a significant portion in industrial settings.
In 2025, the question isn’t just about preventing accidents but about adapting to advancements and emerging challenges in worker safety. What trends, technologies, and regulations are shaping the future of workplace safety?
Key Points:
- Emerging technologies are reshaping safety protocols.
- Regulatory changes demand proactive compliance.
- Health-focused equipment reduces risks.
- Employee education remains critical.
- Organizational culture impacts safety outcomes.
Evolving Safety Priorities for Workers in the Manufacturing Industry
Worker safety priorities in 2025 focus on two key aspects: prevention and compliance. The cost of equipment, such as filtration systems, is a central concern. For example, baghouse price often becomes a decisive factor in implementing air quality solutions. The investment, however, contributes directly to protecting workers from harmful airborne particulates, improving overall workplace safety.
Manufacturers now emphasize worker well-being beyond accidents by addressing long-term hazards like poor air quality and exposure to harmful chemicals. This shift aligns with global efforts to promote sustainable practices while ensuring worker protection.
How Technology is Making Workplaces Safer
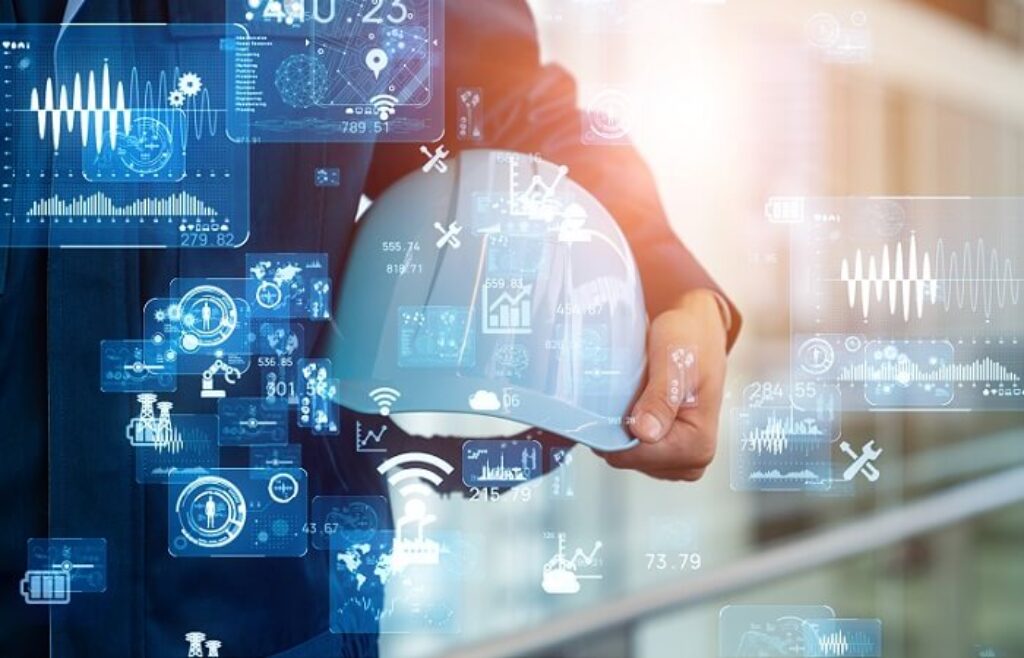
Source: nsc.org
Technological advancements have introduced tools and systems that significantly enhance workplace safety. Below are some examples of revolutionizing worker protection:
- IoT-based safety monitoring systems ─ Wearable devices now monitor vital signs, alerting managers when conditions become unsafe. Sensors track temperature, air quality, and noise levels, providing real-time data to prevent hazardous situations.
- Automation to minimize hazard exposure ─ Robots and automated systems are increasingly performing tasks that expose workers to dangerous environments. Machines reduce the risk of injuries in sectors like welding, chemical handling, and heavy machinery operations.
- Augmented reality (AR) in training programs ─ AR tools provide hands-on, immersive safety training, enabling workers to navigate risk scenarios in virtual settings. This approach improves skills while minimizing accidents during learning periods.
Regulatory Changes in 2025 and Their Impact on Workplace Safety
New compliance standards emphasize worker rights and stricter safety enforcement. Governments across the globe are implementing measures to address critical issues, such as:
- Air quality standards ─ Employers must reduce exposure to harmful airborne substances through advanced filtration systems and ventilation improvements.
- Noise protection requirements ─ Regulations now demand greater protection against hearing loss, including mandatory ear protection devices and soundproofing measures in noisy facilities.
- Mental health provisions ─ A growing number of policies require employers to include mental health resources and stress management programs as part of safety plans.
Non-compliance with updated regulations often leads to significant financial penalties and reputational damage, making adherence a top priority for employers.
The Role of Data in Shaping Safer Work Environments
Data collection and analysis are playing a larger role in workplace safety. Advanced systems now provide actionable insights to reduce risks. Below are ways data is shaping safer environments:
- Predictive analytics ─ Tools that analyze past incidents to identify patterns and potential risks.
- Real-time monitoring ─ Sensors and wearable devices collect data to alert workers and managers about unsafe conditions.
- Performance metrics ─ Tracking safety performance helps organizations measure progress and refine strategies.
Data-driven decision-making empowers businesses to prevent accidents and improve compliance.
Promoting a Proactive Safety Culture
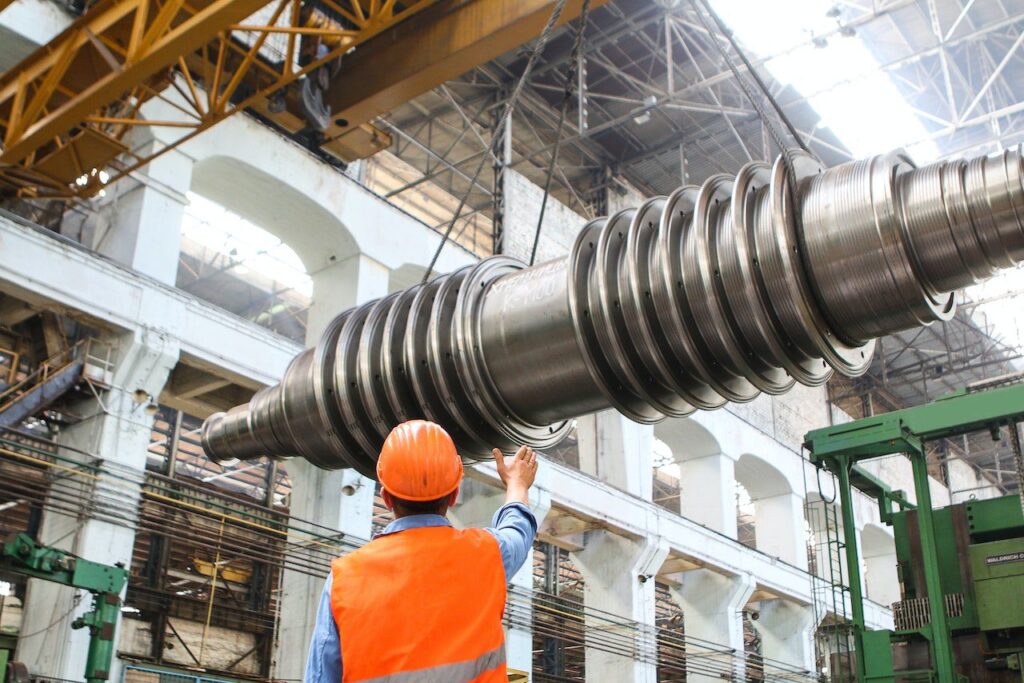
Source: strategydriven.com
Technology and regulations alone cannot create a safer workplace. Leadership must foster an environment where safety is a shared responsibility. Practical ways to encourage a proactive culture include:
- Daily safety meetings ─ Short, focused discussions help reinforce safety protocols and encourage workers to voice concerns.
- Incentive programs for safe practices ─ Rewards for accident-free performance motivate teams to adhere to safety guidelines.
- Accessible reporting systems ─ Simplified tools for reporting hazards encourage workers to highlight issues without fear of repercussions.
When this becomes part of daily operations, organizations not only reduce risks but also improve morale and productivity.
Health-Centered Equipment ─ Investments Worth Making
Equipment investments in 2025 prioritize worker health as much as productivity. Below are tools that are gaining traction:
- Filtration systems ─ Units like baghouses remove harmful dust and particulates, preventing respiratory issues.
- Ergonomic workstations ─ Adjustable equipment minimizes strain-related injuries, especially in repetitive tasks.
- Smart helmets ─ Advanced helmets monitor environmental conditions and provide real-time alerts for hazards.
Businesses that invest in such tools often see reduced insurance claims and improved worker retention rates, making it a cost-effective choice in the long run.
Worker Education ─ Bridging the Knowledge Gap
Education remains a cornerstone of workplace safety. Employees who understand risks and proper protocols can make decisions that prevent accidents. Here are strategies for effective education:
Onboarding Safety Programs
New workers should undergo comprehensive training before starting roles. This approach builds awareness of risks and proper procedures early.
Annual Refreshers
Regularly updating safety knowledge ensures workers stay informed about new tools, policies, and hazards.
Multilingual Resources
Providing materials in multiple languages ensures inclusivity and better understanding among diverse teams.
Well-trained employees are confident and capable, directly reducing accidents across facilities.
Top Worker Safety Trends to Watch in 2025
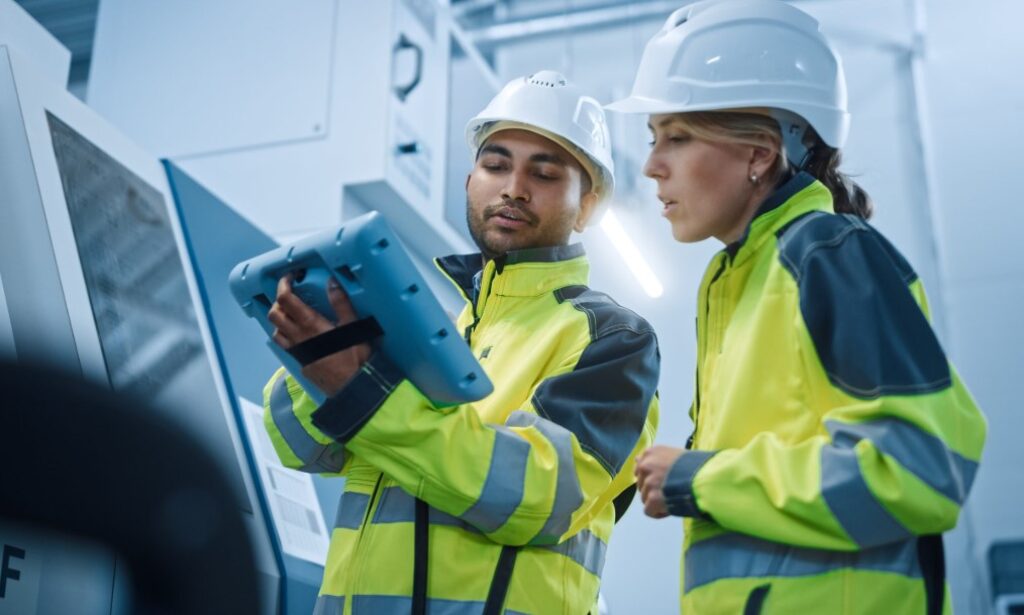
Source: trainanddevelop.ca
Trends in workplace safety reflect a shift toward integrating health, technology, and culture. Below are the key developments:
- Wearable safety tech ─ Devices tracking physical health are becoming widespread.
- AI-powered risk assessment ─ Predictive tools analyze workplace conditions to prevent accidents before they occur.
- Focus on mental health ─ Programs addressing burnout and stress will play a significant role.
- Enhanced PPE ─ Modernized equipment offers better protection without hindering mobility.
- Data-driven insights ─ Real-time analytics help managers identify and mitigate risks immediately.
Organizations embracing these trends position themselves as leaders in worker protection, attracting top talent and maintaining a competitive edge.
Practical Tips for Manufacturing Leaders
Employers seeking to enhance workplace safety in 2025 should focus on practical steps. Below are actionable tips:
- Conduct frequent safety audits to identify and resolve hazards.
- Invest in advanced filtration systems and air-quality monitoring tools.
- Foster open communication to encourage workers to report issues.
- Partner with vendors offering training programs and updated safety equipment.
- Set clear goals for safety performance and regularly review progress.
By focusing on these areas, manufacturers can ensure compliance while creating safer environments for workers.
Concluding Thoughts
The future of worker safety hinges on a combination of innovation, regulation, and culture. Technology offers tools to prevent hazards, but true progress depends on organizations taking proactive steps. Leadership must view this as a continuous process, not a one-time project. By doing so, they protect workers and position their organizations for long-term success in a rapidly evolving landscape.