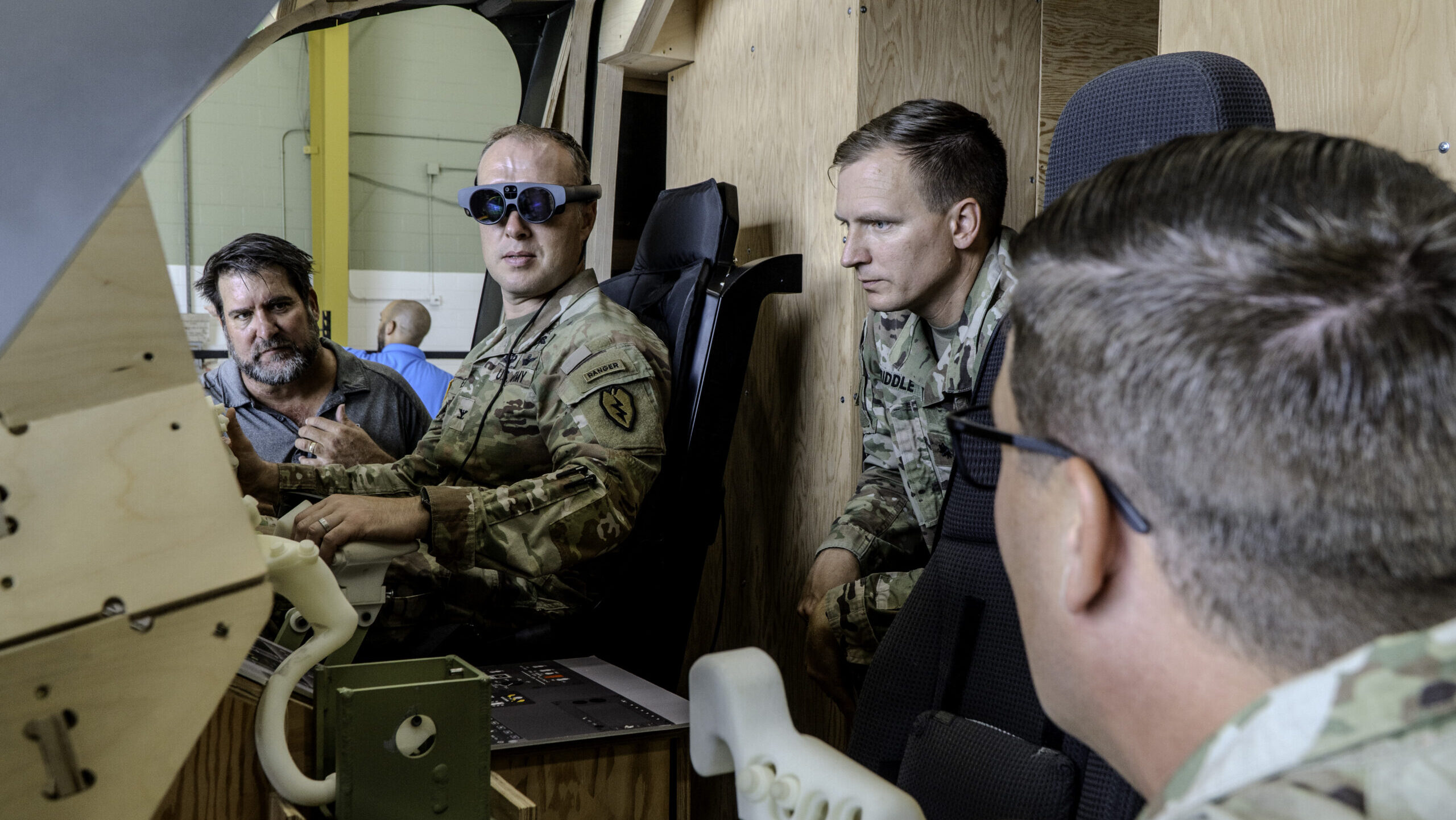
The Future Long Range Assault Aircraft (FLRAA) team show Col. Matthew Scher, the 25th Combat Aviation Brigade commanding officer, what his Soldiers can expect from the FLRAA in the 3rd Battalion, 25th Aviation Regiment hangar Sept. 9, 2024. A tiltrotor aircraft, FLRAA will have the hybrid capabilities of planes and helicopters. (Photo by Spc. Charles Clark, 25th Infantry Div.)
Risk is a program killer, most recently leading to the demise of the Army’s Future Attack Reconnaissance Aircraft that planned for a new platform in addition to a greenfield engine. In contrast, its program-mate under the Future Vertical Lift (FVL) program – the Future Long-Range Assault Aircraft (FLRAA) – is taking an iterative path that places a reliance on mature and high-TRL systems already flying on the the Apache, Black Hawk, and Chinook, including an upgraded but established powerplant, to augment development of new, advanced capabilities such as launched effects.
There’s something else noteworthy about the FLRAA program – it will introduce a tiltrotor to the Army’s aviation fleet for the first time. That in of itself will open new paths to risk throughout the defense industrial base as suppliers design, build, and support systems for FVL, while also creating new opportunities for technology insertion into an aging fleet.
“The last developmental rotorcraft [in the Army was] about 40 or so years ago,” said FLRAA Project Manager Col. Jeffrey Poquette. “So, yes, there are challenges and at the forefront are the industrial base and supply chain risk. This was highlighted during COVID, how fragile the supply chains are – everything from cars to electronics. On the defense side, we’ve seen it with ammunition and now with aircraft, which is a very complex weapon system with a lot of components.
“I wouldn’t say that there are unique challenges particular to a tiltrotor. A tiltrotor is a kind of rotorcraft, a helicopter is a kind of rotorcraft, and both of them have complex supply chains that we have to manage carefully. Ensuring a resilient supply chain has been at the forefront of this program for many years now. We’ve stood up a supply chain risk management team that looks at everything from the raw materials to finished products and subcomponents [at] the lowest level in the supply chain.”
In addition, a relatively recent DoD-wide acquisition capability called “consent to subcontract” gives project managers and contractor officers greater control over subcontracts that their prime contractors award to their lower-tier subs. In the case of FLRAA, Bell is the prime.
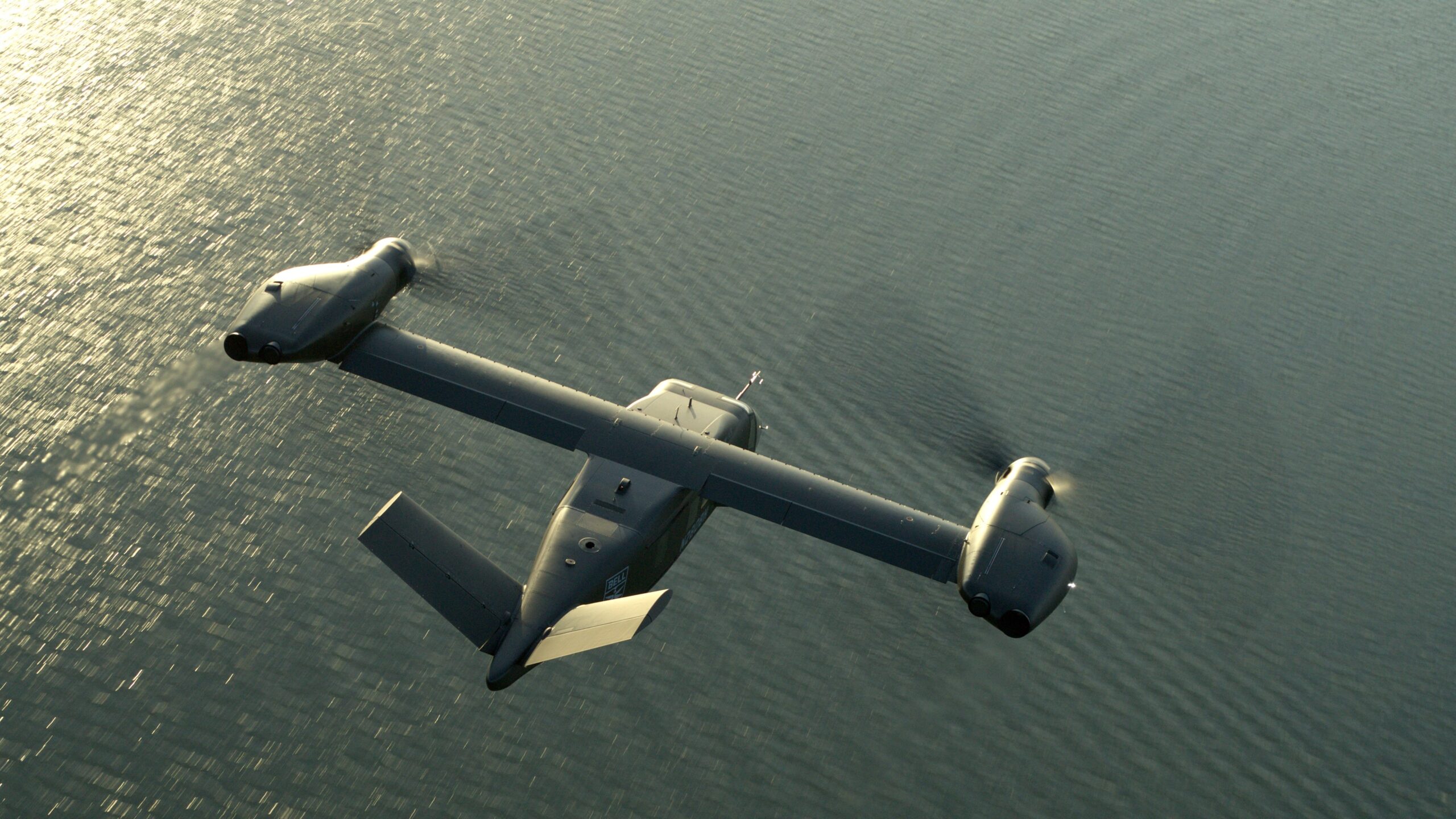
The FLRAA tiltrotor is now in the Engineering and Manufacturing Development phase where the critical design of the aircraft will be finalized, leading to development of aircraft prototypes for testing. (Bell photo)
“When Bell wants to subcontract with a supplier, they have to prove out a number of things, and one is supply chain resilience and risk level,” said Poquette, noting areas of particular concern that include whether suppliers rely on raw materials that can only be sourced from outside the U.S., and if they’ve developed multiple sources of supply within their own lower-tier suppliers. “My team then assesses it and before I sign off on that consent, we take a look at supply chain risk management.”
FLRAA’s Milestone B decision attained in mid-2024 was, in part, due to the program’s risk posture at that point. The tiltrotor is now in the Engineering and Manufacturing Development phase where the critical design of the aircraft will be finalized, leading to development of aircraft prototypes for testing, ultimately informing a Milestone C decision in 2028 about production of fieldable aircraft.
“Supply chain risk management is key to a healthy production line,” said Ryan Ehinger, senior vice president and program director, FLRAA Future Long Range Assault Aircraft/V-280 Valor at Bell. “Aviation component lead times are long and requalification/switching costs for making changes mid-production are high. The government and industry collectively have done a tremendous amount of work over the last decade to reduce risk and inform the requirements, and the current EMD phase is all about further maturation of the digital models, finalizing engineering hardware and software designs, maturing the sustainment artifacts, and driving toward a successful weapon system critical design review as the next major program milestone.
“Bell takes pride in the internal vertical integration of many key components and final assembly, but it is a team of industry leaders spanning many layers of the supply chain that complete the weapon system. All parts are important, and each supplier should feel the weight of program success on their shoulders and an accountability to the warfighters who need this affordable and sustainable capability. We are all working together in EMD, developing myriad systems and components in parallel for integration into our models and assembly and test against the requirements set.”
Who gets the IP?
In addition to risk reduction, the disposition of Intellectual property rights for FLRAA systems is another supply chain issue – who owns what and for how long, and the Army’s desire to prevent vendor lock on systems so new capabilities to address evolving threats can be more quickly spiraled in via the application of the Modular Open Systems Approach (MOSA). The Army says it doesn’t want to own or control all the IP, only where it fits with the Army aviation mission, especially as it relates to sustainment.
“IP for the Army is focused around logistics functions like training, maintaining, sustaining,” said Poquette. “We have the heritage of wanting to be able to do that without reliance on contractor support, especially where the Army operates deep in areas that are considered hazardous. So how did we do that?
“Rather than ask for specific IP, we presented to the contractors what it is we wanted to do. We did that in hundreds of use cases. We need to be able to develop training materials and manuals, we need to be able to change them when it’s time to change them. We need to be able to instruct and train on how to do maintenance. What we did was incentivize the contractors during competition to provide the most that they could in order to meet those use cases. Once we had a winner in the competition, we signed Bell up to provide all that intellectual property,” he said, adding that this has been an effective way to get access to the appropriate amount of IP that the Army needs while still protecting the creators of that IP.
Such strategies around MOSA, intellectual property, and data rights for FLRAA’s long-term sustainment are a significant shift that will impact how suppliers have traditionally operated their businesses.
Said Ehinger, “With some of these new initiatives, suppliers that are able to provide the best value in a competitive environment will do well and suppliers that fail to adapt will see fewer opportunities. A key element of this requires collaboration between industry and government to understand associated intellectual property and data rights, what is needed for long-term organic sustainment, and how industry can help facilitate that. Customers are rightfully passionate about their ability to sustain their platforms over the long term. MOSA is going to be a game changer in terms of enabling affordable upgrades to mission systems.
“As an industry we are at a unique time where we can create a truly new weapon system leveraging the latest in manufacturing technology to yield improvements in affordability and quality. Part of this is due to the advancement in machinery, as well as how the digital thread and software has matured to allow fewer steps in the transition from engineering to manufacturing to assembly and inspection, all leveraging the same source data and reducing the opportunity for defective data. The industrial base is advancing to embrace this and, from a supply chain perspective, those that are able to thrive in this environment of model-based definition and maintain the integrity of the digital thread are at a clear advantage.”